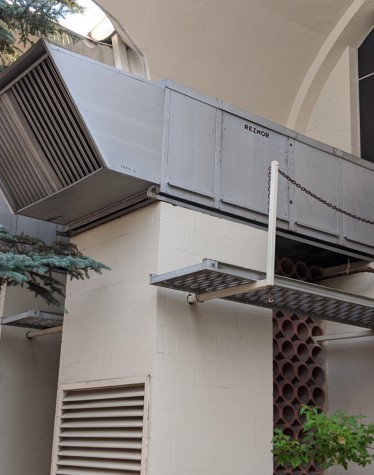
Building Systems, COVID-19, and Colorado College
Recently, a lead engineer at Colorado College reached out to Farnsworth Group for support. Faced with increasing pressure to maintain a safe environment, re-occupy spaces, and provide peace of mind to decision makers that industry standards were being followed, he needed some additional resources.
This was a great team collaboration! Our team plan utilized work-sharing opportunities among some of our brightest young engineers in the commissioning and MEP departments. At the end of the day everyone worked well together and delivered more than what the client expected.
The technical requirements for any building assessment can be daunting, not to mention one that involves 16 buildings and over 1.3 million square feet of building area. (That’s equivalent to over 27 football fields!) And then there’s the pressure of time: in order to provide results to key stakeholders and shift budgets for capital allocations, the project needed to be completed within six weeks. Furthermore, the complexity was apparent. This was not a run-of-the-mill HVAC study, but needed to answer specific questions like:
- What recommendations from the industry (think ASHRAE Position Document on Infectious Aerosols) apply to these buildings?
- How can I retrofit existing systems to save cost and improve safety?
- What data do I need to collect to run the calculations to increase the outdoor fresh air intake for this facility?
- How do we provide specific and efficient recommendations that address the unique needs of each of the 16 buildings into a report that makes sense to a non-technical audience?
Truly, these are the types of projects that Farnsworth Group engineers are perfectly equipped to tackle.
We quickly mobilized a four-person team. Prior to rushing to the site and analyzing the equipment, the team immediately saw this assessment as an opportunity to tackle a few other priorities that the College faced – while still meeting the project schedule and budget. Knowing that the College has a myriad of building vintages and all sorts of shapes and sizes of equipment, the College had also brought a Test and Balance (TAB) contractor and Building Automation System (BAS) controls technician on board to complement our team. Having the ability to fix issues on the spot would ultimately save the College a tremendous amount of time and money. The College was essentially getting a retro-commissioning study along with a COVID risk assessment which offered more value with the same amount of effort.
In the end, the team worked to utilize as much from the existing equipment as possible. Where needed, recommendations for capital purchases were cost-effective and justified - as if the team were paying for these out of their own wallet.
Recommendations included increasing ventilation rates and filtration efficiencies, changing motor sheaves, adjusting outdoor air damper settings, modifying filter racks, and implementing new technologies, like bi-polar ionization, where effective. The client received a list of recommendations, easily understood by a non-technical decision maker, and a better understanding of the limits of their HVAC systems when addressing airborne virus transmission.
Additionally, the College benefitted because all of this happened while correcting over 60 issues during inspections. The report was not another action list, but rather, a summary of items corrected and clear direction regarding how to best focus their limited budget dollars.